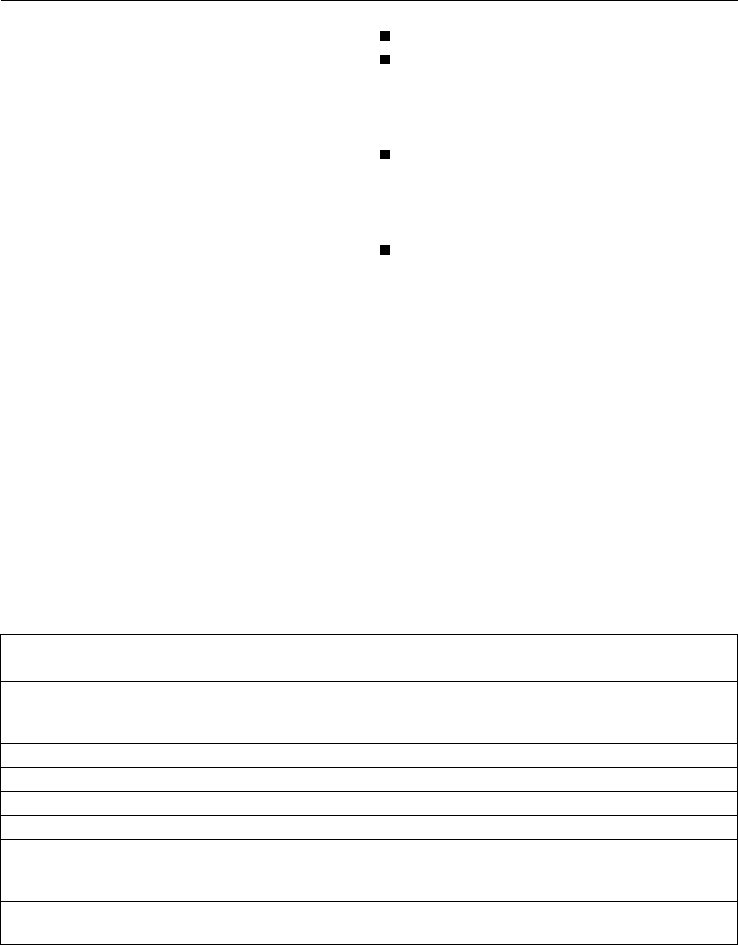
The shorter the exhaust ductwork, the
more efficient the dryer will be. Ex-
pelled air is slowed down in the ducts
due to friction against the inner walls,
therefore the shorter and smoother the
inner walls are, the less friction will
occur.
An elbow or bend creates more friction
than a straight duct. An additional duct
length factor must therefore be added
for each elbow or bend (see Table I).
This factor expresses the resistance of
the bend in terms of a straight length of
duct.
The additional length factor is then
added to the measured duct length to
give the effective duct length.
A larger duct diameter also helps to re-
duce friction. The duct diameter should
therefore be increased with increasing
duct length.
To calculate the effective duct length.
Measure the actual duct length.
Establish the number of elbows or
bends necessary, noting the type of
bend, angle and radius involved
(see Table I).
Add the additional length factor as
specified in Table I to the actual duct
length to give the effective duct
length.
The necessary duct diameter should
then be found in Table II.
Note:
Drying times and energy consumption
remain unaltered for 100 mm duct up
to a total length of 10 m.
Longer duct may lead to slight in-
creases in drying times and energy
consumption but will not impair the
function of the machine as long as the
necessary duct diameter is used (see
Table II).
Tabel I
Type of bend Angle Radius in mm Additional duct
length in m
Flexible metal piping 90°
90°
45°
100-300
300-500
100-500
0.5
0.4
0.4
Plain piping 90° 100 0.4
Elbow 2.5
Concertina bend 90° 200 0.8
Segmented bend 90° 200 0.6
Wall vent kit with louvres, or window vent kit
Wall vent kit with flap, or window vent kit
3.8
1.5
Exhaust connection, left/right side
Flat section adaptor
6/10
8
Installation - venting
22